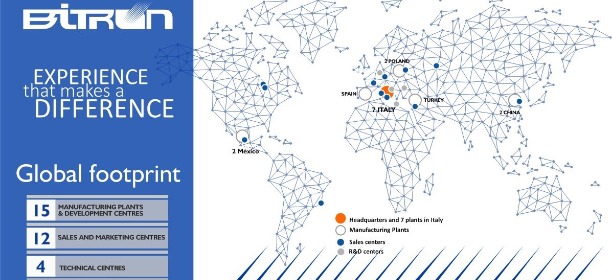
QUALIFICATIONS AND JOB DESCRIPTION
Bitron Group is a global privately held company leader in research, development and manufacturing of mechatronic devices and systems for the automotive, appliance, HVAC, charging systems for electrical vehicle, medical and energy industries.
The plants are in Italy, Poland, China, Mexico and Turkey representing a competitive footprint with global localization.
Around 7200 skilled employees, Bitron Group continues production of the most innovative technologies.
Bitron Group, in order to grow the capabilities, is currently looking for:
Process Quality Control Engineer
Qualifications
- Graduate degrees from Electric-Electronic Eng.
General skills
- Knowledge of English language,
- Ability to interpret a technical drawing (reading dimensions, tolerances, view interpretation) and specific requirements,
- In-depth knowledge of company production details, their production processes and related criticalities,
- Knowledge of measuring/control and testing instruments used on specific products and their use,
- Critical observation skills, analytical skills, decision-making and management skills in critical conditions, meticulousness and good manual dexterity,
- Ability to relate to the customer and other business entities, aptitude for dialogue and good dialectics,
- Knowledge of process auditing techniques,
- Knowledge of computer tools,
- No military obligation for male candidates,
- No travel restriction.
Job Definition
- Examines and records the complaint received and any returned products associated with it. Performs the technical analysis of the returned part, directly or by using the technical support of other company or external bodies (laboratories), subjecting all parts to specific tests to define the defect in detail (defective component, type of defect),
- Verifies if and which products in the field/ at the customer's site/ warehouse/ in process are affected by the complaint and then activates the appropriate response program to handle the non-conformity,
- Prepares a written response to be sent to the Customer, in the form of a plan of activities following the complaint, which may be preliminary or final depending on the progress of the analysis of the defect, identification of the causes and their elimination through appropriate corrective actions,
- Encodes the detected defect in order to monitor the evolution of the problem over time,
- Basing on specific prescriptions, indications and drawings, and with the aid of measuring instruments, verifies the physical and functional characteristics of internally produced parts,
- Identifies the most critical characteristics in the various products and in the various phases of the production process to be included in the control,
- Ensures that all products subjected to control are compliant to specified requirements,
- Effectively prepares suitable treatments to remove causes of non-conformity,
- Performs audits on the production lines, to verify the correct performance of activities to ensure the quality of production, to approve new lines and to promote improvement actions,
- Intervenes on timely criticalities that may arise during the production process.